Also Read
VIVA QUESTIONS :
Q1: Define welding?
Ans: Welding is a fabrication process that joins two or more materials, typically metals or thermoplastics, by melting and fusing them together using heat or pressure.
Ans: Welding is a fabrication process that joins two or more materials, typically metals or thermoplastics, by melting and fusing them together using heat or pressure.
Q2: What is the typical thickness of MS Plate used in general welding workshop experiments?
Ans: The thickness of the MS (Mild Steel) plate used in general welding workshop experiments can vary depending on the specific requirements of the experiment. However, commonly used thicknesses range from 3 mm to 12 mm.
Q3: What is the common job material used in welding experiments?
Ans: The common job material used in welding experiments is mild steel. It is widely available, affordable, and relatively easy to work with, making it suitable for various welding applications and practice.
Q4: What is the main function of an electrode in welding?
Ans: The main function of an electrode in welding is to carry the electric current necessary for the welding process and to provide filler material to create the weld joint. It melts and deposits the metal into the joint to form a strong bond.
Q5: What is the use of a flat file in welding?
Ans: A flat file is used in welding for the purpose of smoothing and shaping metal surfaces. It helps in removing burrs, sharp edges, and excess material from the welded joint to achieve the desired finish.
Q6: For what purpose do you use a scriber in welding?
Ans: A scriber is used in welding to mark lines or measurements on the surface of the workpiece. It helps in accurately positioning and aligning the metal pieces before welding.
Q7: While performing electric arc welding, what safety device is used to protect your eyes from sparks?
Ans: A welding helmet or welding mask with a suitable shade lens is used to protect the eyes from sparks, intense light, and harmful radiation emitted during electric arc welding.
Q8: What type of welding have you done in the workshop lab?
Ans: The type of welding conducted in the workshop lab may vary depending on the specific curriculum or training program. However, common types of welding done in workshop labs include Shielded Metal Arc Welding (SMAW), Gas Metal Arc Welding (GMAW), and Gas Tungsten Arc Welding (GTAW).
Q9: When the workpiece is hard, what holding tool is used to carry it?
Ans: When the workpiece is hard, a vise or clamp is commonly used as a holding tool to secure and carry it. The vise provides a stable grip on the workpiece, allowing for accurate welding operations.
Q10: What is the sequence of operations in welding?
Ans: The sequence of operations in welding typically involves the following steps:
- Preparing the workpiece, such as cleaning and removing any contaminants.
- Positioning and aligning the workpiece and securing it in place.
- Selecting the appropriate welding process, setting the welding parameters, and preparing the equipment.
- Striking an arc or initiating the welding process.
- Controlling the welding process while maintaining the desired arc length, heat input, and welding speed.
- Inspecting the completed weld for quality and making any necessary adjustments or finishing operations.
Ans: In the welding process, the cathode is typically connected to the workpiece or the metal being welded. The electrode is connected to the positive terminal or anode.
Q12: What do you mean by cathode and anode in welding?
Ans: In welding, the cathode refers to the negatively charged electrode or workpiece, while the anode refers to the positively charged electrode. The cathode is where the reduction reaction occurs, and the anode is where the oxidation reaction occurs during the welding process.
Q13: As a result of welding, a black bead is formed. What is its name?
Ans: The black bead formed as a result of welding is commonly known as the slag. It is a layer of non-metallic residue that forms on the surface of the weld and protects it from atmospheric contamination during the cooling process.
Q14: How is slag removed in welding?
Ans: Slag is typically removed in welding by chipping or using a wire brush. After the weld has cooled down, the slag layer is carefully chipped away using a hammer and chisel, or a wire brush is used to clean and remove the slag residue from the welded joint.
Q15: What is the difference between a butt joint and a lap joint?
Ans: A butt joint is a type of joint where the ends of two metal pieces are aligned and joined together in a single plane, forming a square or beveled edge. In contrast, a lap joint is a type of joint where one metal piece overlaps the other, creating a double thickness at the joint.
Q16: What is the purpose of a try square in welding?
Ans: A try square is used in welding to ensure the accuracy and perpendicularity of the joint. It helps in checking the alignment and squareness of the welded components or pieces.
Q17: What is the purpose of a bench vice in welding?
Ans: A bench vice is a clamping tool used in welding to hold the workpiece securely during welding operations. It provides stability and allows for precise positioning and alignment of the workpiece.
Q18: Why is slag formed in welding?
Ans: Slag is formed in welding due to the flux coating on the electrode. The flux is designed to protect the weld from atmospheric contamination by creating a layer of slag. The slag acts as a shield, preventing oxygen and other impurities from reacting with the molten metal.
Q19: What are the electrode materials used in welding?
Ans: Electrodes used in welding can be made of various materials depending on the specific welding process and application. Common electrode materials include mild steel, stainless steel, cast iron, aluminum, and various alloys.
Q20: How do you perform finishing operations in welding?
Ans: Finishing operations in welding typically involve cleaning the weld joint, removing any sharp edges or burrs, and achieving the desired surface smoothness. This can be done using various tools such as grinding wheels, sandpaper, files, or wire brushes.
Q21: Why is coating necessary in an electrode?
Ans: Coating is necessary in an electrode to provide specific properties and functions during the welding process. The coating can provide protection against atmospheric contamination, stabilize the arc, control the weld pool, and add alloying elements to improve the weld's mechanical properties.
Q22: Which material is coated on the electrode?
Ans: The coating material on the electrode can vary depending on the specific type of electrode and its intended use. It may include various compounds such as fluxes, binders, stabilizers, and alloying elements tailored to the specific welding process and application.
Q23: What type of electricity is used in arc welding?
Ans: In arc welding, either direct current (DC) or alternating current (AC) can be used depending on the welding process and the type of material being welded. DC is commonly used for most welding applications, while AC is often used for welding aluminum and some specialized applications.
Q24: What is the tool used to cut the MS Flat?
Ans: The tool used to cut the MS (Mild Steel) flat is typically a cutting machine such as an angle grinder, oxy-fuel torch, plasma cutter, or a power hacksaw.
Q25: What are the different types of welding processes?
Ans: There are several types of welding processes, including:
- Shielded Metal Arc Welding (SMAW)
- Gas Metal Arc Welding (GMAW)
- Gas Tungsten Arc Welding (GTAW)
- Flux-Cored Arc Welding (FCAW)
- Submerged Arc Welding (SAW)
- Resistance Spot Welding (RSW)
- Laser Welding
- Electron Beam Welding (EBW)
Ans: The basic components required for arc welding are:
- Power source
- Electrode holder and cable
- Ground clamp and cable
- Welding electrode or filler material
- Protective equipment (e.g., helmet, gloves, apron)
Ans: Some safety precautions during welding include:
- Wearing appropriate protective gear (helmet, gloves, clothing)
- Ensuring proper ventilation in the welding area
- Using welding screens or curtains to protect nearby workers
- Keeping a fire extinguisher nearby
- Checking the welding equipment for any defects before starting
- Following proper electrical and grounding procedures
- Being aware of the hazards associated with welding fumes and UV radiation
Ans: A welding electrode is used to carry the electric current necessary for the welding process and to provide filler material to create the weld joint. It melts and deposits the metal into the joint to form a strong bond.
Q29: What is the difference between AC and DC welding?
Ans: AC (alternating current) welding and DC (direct current) welding refer to the type of electrical current used in the welding process. AC welding is often used for welding aluminum and magnesium alloys, while DC welding is commonly used for steel and stainless steel. The choice between AC and DC depends on the material being welded and the specific requirements of the welding process.
Q30: What is the purpose of a shielding gas in welding?
Ans: Shielding gas is used in certain welding processes, such as gas metal arc welding (GMAW) and gas tungsten arc welding (GTAW), to protect the weld pool and electrode from atmospheric contamination. The gas forms a protective shield around the weld, preventing the molten metal from reacting with oxygen, nitrogen, or other elements in the air, which could weaken the weld or cause defects.
Q31: What is the purpose of a welding helmet or welding mask?
Ans: The purpose of a welding helmet or welding mask is to protect the welder's face, eyes, and neck from sparks, intense light, and harmful radiation emitted during welding. It also provides a clear and tinted view of the welding area for the welder to perform their work safely.
Q32: What is the difference between MIG welding and TIG welding?
Ans: MIG (Metal Inert Gas) welding and TIG (Tungsten Inert Gas) welding are two different welding processes. In MIG welding, a continuously fed consumable wire electrode and a shielding gas are used to create the weld. TIG welding, on the other hand, uses a non-consumable tungsten electrode and a separate filler material, if needed. MIG welding is faster and more suitable for thicker materials, while TIG welding allows for more precise and high-quality welds on thinner materials.
Q33: What is the purpose of a chipping hammer in welding?
Ans: A chipping hammer is used in welding to remove slag, spatter, and other impurities from the weld surface. It has a chisel-like end that allows the welder to chip away the unwanted material after welding.
Q34: What is the role of flux in arc welding?
Ans: Flux is a material that is often used in arc welding processes such as shielded metal arc welding (SMAW) and submerged arc welding (SAW). It acts as a shielding agent and provides a protective layer over the weld pool, preventing oxidation and atmospheric contamination. Flux also helps in stabilizing the arc and controlling the weld's properties.
Q35: What are the advantages of using gas shielding in welding?
Ans: Gas shielding, as used in processes like gas metal arc welding (GMAW) and gas tungsten arc welding (GTAW), offers several advantages in welding. It helps to protect the weld area from atmospheric contamination, prevents oxidation and porosity in the weld, provides better arc stability, and improves the overall quality of the weld.
Q36: What is the purpose of a welding ground clamp?
Ans: A welding ground clamp is used to establish a proper electrical connection between the workpiece and the welding power source. It ensures a safe and efficient flow of electric current during welding and helps in creating a stable welding arc.
Q37: How is a fillet weld different from a groove weld?
Ans: A fillet weld is a weld joint where two pieces of metal are joined at an angle to form a triangular fillet-shaped weld. It is commonly used for lap joints, T-joints, and corner joints. A groove weld, on the other hand, is a weld joint where a groove or channel is prepared in the metal pieces, and the weld is deposited in the groove. Groove welds are typically used for butt joints.
Q38: What is the purpose of a welding positioner?
Ans: A welding positioner is a device used to manipulate the position and orientation of the workpiece during welding. It allows the welder to rotate, tilt, or move the workpiece to achieve better access, visibility, and control over the welding process. This helps in producing consistent and high-quality welds, particularly in complex or overhead welding situations.
Q39: What is the difference between a welder and a welding operator?
Ans: A welder is an individual who performs the physical welding operations. They operate the welding equipment, prepare the workpieces, and execute the welding process. A welding operator, on the other hand, is responsible for setting up and adjusting the welding equipment, selecting appropriate welding procedures, and ensuring that the welder follows the specified guidelines and standards.
Q40: What are some common defects that can occur in welds?
Ans: Some common defects in welds include porosity (voids or gas pockets), lack of fusion (incomplete bonding between the base metal and the weld), cracks, undercutting (excessive melting of the base metal at the weld edges), and excessive spatter. Other defects may include distortion, improper weld size, and slag inclusions. These defects can affect the strength, integrity, and quality of the weld joint.
Q41: What safety precautions should be taken during welding?
Ans: Several safety precautions should be followed during welding, including:
- Wearing appropriate personal protective equipment (PPE) such as a welding helmet, safety glasses, welding gloves, and protective clothing.
- Ensuring proper ventilation or using respiratory protection to prevent inhalation of welding fumes and gases.
- Maintaining a clean and organized work area to prevent tripping hazards and fire risks.
- Using proper welding techniques and equipment settings to minimize the risk of accidents and injuries.
- Following electrical safety guidelines, including proper grounding of equipment and avoiding contact with live electrical parts.
- Being aware of fire hazards and having fire extinguishing equipment nearby.
- Adhering to safety regulations and guidelines provided by the welding industry and relevant authorities.
Ans: Preheating is the process of heating the base metal before welding. It is done to reduce the cooling rate and control the temperature gradient during welding, especially for materials with high carbon content or high susceptibility to cracking. Preheating helps in reducing residual stresses, improving weldability, and minimizing the risk of weld defects.
Q43: What is the difference between a single-pass weld and a multipass weld?
Ans: A single-pass weld is a weld joint that is completed in a single welding pass, where the entire weld is deposited in a single operation. A multipass weld, on the other hand, requires multiple welding passes to complete the joint, with each pass adding a layer of weld metal until the desired weld size and strength are achieved. Multipass welding is often required for thicker materials or when specific welding procedures call for it.
Q44: What is the purpose of post-weld heat treatment (PWHT)?
Ans: Post-weld heat treatment (PWHT) is a controlled heating and cooling process applied to a welded joint after welding. It is done to relieve residual stresses, improve the mechanical properties of the weld and the base metal, and reduce the risk of cracking or distortion. PWHT is commonly used in specific applications or for certain materials that require additional treatment to achieve desired properties.
Q45: What are some common welding defects that can occur in the weld metal itself?
Ans: Some common welding defects that can occur in the weld metal include excessive penetration, insufficient penetration, improper weld size, incomplete fusion, cracks (such as hot cracks or cold cracks), and inclusions (such as slag or oxide inclusions).
Q46: What is the purpose of a welding electrode holder?
Ans: The welding electrode holder is a tool used to hold and control the welding electrode during manual arc welding. It provides a secure grip on the electrode and allows the welder to position and manipulate it within the welding joint.
Q47: What are the different types of welding positions?
Ans: The different types of welding positions include flat position (1G), horizontal position (2G), vertical position (3G and 4G), and overhead position (4F). These positions refer to the orientation of the weld joint and determine the direction of welding and the welding techniques used.
Q48: What is the purpose of a welding regulator?
Ans: A welding regulator is a device used to control and regulate the flow of gases, such as shielding gases or fuel gases, during welding. It ensures a consistent and precise flow rate, maintaining the required gas pressure for optimal welding conditions.
Q49: What is the purpose of a welding nozzle or welding tip?
Ans: A welding nozzle or welding tip is a component of a welding torch used in gas welding and cutting processes. It directs and controls the flow of the welding or cutting gas, shaping the flame and providing stability and precision during the welding or cutting operation.
Q50: What is the purpose of a welding blanket or welding curtain?
Ans: A welding blanket or welding curtain is a fire-resistant protective covering used to shield the surrounding area from sparks, heat, and spatter generated during welding. It helps prevent accidental fires, protects nearby objects or surfaces, and ensures a safe working environment.
Q51: What is the purpose of a welding positioner?
Ans: A welding positioner is a device used to rotate, tilt, or manipulate the workpiece during welding. It allows the welder to position the workpiece at a comfortable and optimal angle, improving access and visibility to the weld joint, and facilitating the welding process.
Q52: What is the purpose of a back purge in welding?
Ans: Back purging is a technique used in welding to provide protection on the backside of a weld joint, particularly in welds that require full penetration. It involves introducing a shielding gas, such as argon, into the backside of the weld joint to prevent oxidation, reduce the risk of weld defects, and ensure sound weld quality.
Q53: What is the purpose of pre-weld and post-weld cleaning?
Ans: Pre-weld cleaning involves the removal of contaminants, such as dirt, grease, oil, rust, or paint, from the surfaces to be welded. It ensures proper fusion and sound welds by promoting good adhesion and minimizing the risk of weld defects. Post-weld cleaning is performed after welding to remove slag, spatter, and other residues from the weld joint, ensuring a clean and visually appealing weld appearance.
Q54: What is the purpose of a welding position indicator?
Ans: A welding position indicator is a device or tool used to measure and indicate the position and alignment of the welding joint during welding. It helps the welder maintain the correct welding position and angle, ensuring proper weld placement and adherence to welding specifications.
Q55: What is the purpose of a welding gauge?
Ans: A welding gauge is a measurement tool used to check and verify various parameters during welding, such as weld size, weld reinforcement, joint dimensions, bevel angle, and groove dimensions. It ensures compliance with welding standards and specifications, facilitating quality control and inspection of welds.
Q56: What is the purpose of a welding positioner?
Ans: A welding positioner is a device used to rotate, tilt, or manipulate the workpiece during welding. It allows the welder to position the workpiece at a comfortable and optimal angle, improving access and visibility to the weld joint, and facilitating the welding process.
Q57: What is the purpose of a welding backing strip?
Ans: A welding backing strip is a material placed on the opposite side of the weld joint to support and contain the molten weld metal. It helps in achieving a sound weld by preventing the formation of undercuts, ensuring proper fusion, and reducing the risk of defects, especially in butt joint welds.
Q58: What is the purpose of a welding positioner?
Ans: A welding positioner is a device used to rotate, tilt, or manipulate the workpiece during welding. It allows the welder to position the workpiece at a comfortable and optimal angle, improving access and visibility to the weld joint, and facilitating the welding process.
Q59: What is the purpose of a welding ground clamp?
Ans: A welding ground clamp is used to establish a proper electrical connection between the workpiece and the welding power source. It ensures a safe and efficient flow of electric current during welding and helps in creating a stable welding arc.
Q60: What is the purpose of a welding joint?
Ans: A welding joint is the area where two or more pieces of metal are joined together by welding. The purpose of a welding joint is to provide a secure and structurally sound connection between the metal pieces, enabling the transfer of loads and maintaining the integrity of the assembled structure.
Q61: What is the purpose of a welding positioner?
Ans: A welding positioner is a device used to rotate, tilt, or manipulate the workpiece during welding. It allows the welder to position the workpiece at a comfortable and optimal angle, improving access and visibility to the weld joint, and facilitating the welding process.
Q62: What is the purpose of a welding helmet?
Ans: A welding helmet is a protective headgear worn by welders to shield their face, eyes, and neck from sparks, intense light, and harmful radiation emitted during welding. It also provides a clear and tinted view of the welding area for the welder to perform their work safely.
Q63: What is the purpose of a welding electrode?
Ans: A welding electrode is a consumable filler metal used in arc welding processes. Its purpose is to conduct electric current and create an arc between the electrode and the workpiece, melting the electrode and forming a weld pool that fuses the base metal and creates a strong joint when solidified.
Q64: What is the purpose of a welding flux?
Ans: Welding flux is a material used in certain welding processes, such as shielded metal arc welding (SMAW) and submerged arc welding (SAW). Its purpose is to provide a protective gas shield around the arc, preventing atmospheric contamination and oxidation of the weld metal. Flux also helps in stabilizing the arc and controlling the weld properties.
Q65: What is the purpose of a welding wire?
Ans: A welding wire, also known as a filler wire or electrode wire, is used in welding processes that involve the melting of a filler metal to join two or more base metals. The purpose of a welding wire is to provide additional material to the weld pool, ensuring proper fusion and creating a strong, reliable weld joint.
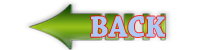
Comments
Please visit Perth plumbing company
we are plasma torches manufacturers in ludhiana punjab.
Please Look Here At Weld Inspection Perth
Arc welding machine Manufacturer in Ludhiana